Difference between JIC and SAE flare fittings
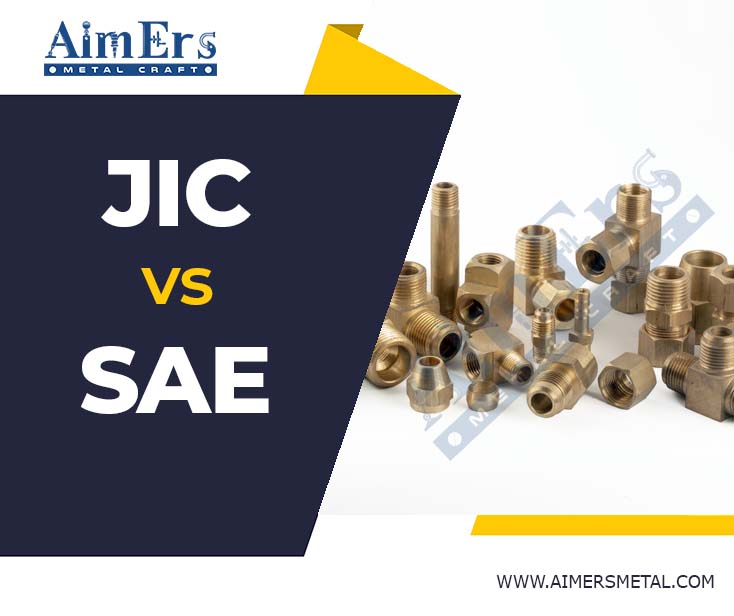
Flare fittings play a crucial role in connecting pipes, tubes, and hoses in various industries, ensuring secure and leak-free connections. Among the different types of flare fittings available, JIC (Joint Industry Council) and SAE (Society of Automotive Engineers) flare fittings stand out. Understanding the difference between these two types is essential for selecting the right fittings for specific applications.
Introduction to Flare Fittings
Flare fittings are widely used in hydraulic systems, plumbing, and automotive applications to connect rigid metal tubing or hoses. These fittings feature a tapered end and a mating flare nut, providing a reliable seal when tightened. The flared end of the fitting forms a metal-to-metal contact with the mating surface, ensuring a leak-resistant connection.
Understanding JIC Flare Fittings
What is JIC?
JIC, or Joint Industry Council, flare fittings are widely used in fluid power applications, including hydraulic systems. These fittings feature a 37-degree flare angle and are known for their versatility and reliability.
How do JIC flare fittings work?
JIC flare fittings create a tight seal by compressing the flare against the mating surface. They are commonly used in high-pressure applications and offer excellent resistance to vibration and mechanical stress.
Applications of JIC flare fittings
JIC flare fittings are commonly found in hydraulic systems, aircraft, industrial equipment, and automotive applications where reliable connections are crucial.
Understanding SAE Flare Fittings
What is SAE?
SAE, or Society of Automotive Engineers, flare fittings are specifically designed for automotive applications, including fuel lines and brake systems. These fittings typically feature a 45-degree flare angle.
How do SAE flare fittings work?
Similar to JIC fittings, SAE flare fittings create a seal by compressing the flare against the mating surface. They are commonly used in automotive systems where resistance to vibration and corrosion is essential.
Applications of SAE flare fittings
SAE flare fittings are primarily used in automotive fuel systems, brake lines, and other hydraulic applications in vehicles.
Differences Between JIC and SAE Flare Fittings
Thread Angle
JIC flare fittings have a 37° flare angle, while SAE flare fittings have a 45° flare angle. This difference in flare angles affects the compatibility between fittings from different systems.
Flare Angle
The flare angle of JIC fittings is smaller compared to SAE fittings, which can impact the sealing performance and compatibility between fittings.
Applications
JIC flare fittings are commonly used in industrial and hydraulic applications, while SAE flare fittings are prevalent in automotive systems.
Standards and Specifications
JIC flare fittings adhere to standards set by the Joint Industry Council, while SAE flare fittings follow specifications outlined by the Society of Automotive Engineers.
Advantages and Disadvantages of JIC Flare Fittings
Advantages:
- Versatility
- Reliable sealing
- Commonly available
Disadvantages:
- Limited compatibility with other systems
- Higher cost compared to some alternatives
Advantages and Disadvantages of SAE Flare Fittings
Advantages:
- Widely used in automotive applications
- Good resistance to vibration and corrosion
Disadvantages:
- Limited compatibility with non-automotive systems
- May require specific tools for installation
When to Use JIC Flare Fittings
SAE flare fittings are best suited for automotive applications, including fuel lines and brake systems.
Best Practices for Installing JIC Flare Fittings
- Ensure proper alignment and cleanliness of mating surfaces.
- Use appropriate torque to achieve a secure connection.
- Inspect fittings for damage or defects before installation
Best Practices for Installing SAE Flare Fittings
- Follow manufacturer guidelines for torque specifications.
- Use flaring tools designed for SAE fittings to achieve proper flare angles.
- Inspect fittings and tubing for signs of wear or damage.
Common Mistakes to Avoid When Working with Flare Fittings
- Over-tightening fittings, which can damage threads and compromise sealing integrity.
- Using mismatched fittings from different systems, leading to leaks and improper connections.
- Neglecting to deburr tubing ends, which can cause leaks and flow restrictions.
Conclusion
In summary, understanding the differences between JIC and SAE flare fittings is crucial for selecting the right fittings for specific applications. While both types offer reliable sealing and performance, their design and specifications cater to different industries and systems. By considering factors such as flare angle, thread compatibility, and application requirements, professionals can ensure proper installation and optimal performance of flare fittings in various settings.
FAQs about JIC and SAE Flare Fittings
While some fittings may be compatible, it’s essential to verify compatibility before mixing components from different systems to prevent leaks and other issues.
While JIC fittings offer reliable sealing and performance, they may not be the best choice for automotive systems due to compatibility issues and specific requirements of SAE standards.
Installation typically requires flaring tools, wrenches, and torque wrenches to ensure proper alignment, sealing, and tightening.
Regular inspection for leaks, damage, and proper torque is essential to maintain the integrity and performance of flare fittings over time.
While some fittings may be reusable, it’s essential to inspect them carefully for damage or wear before reinstallation to.